Deep Dive into Trusted Pre-Press Products from EXILE
- Caroline Kempf
- Sep 21, 2023
- 4 min read
Updated: 7 days ago
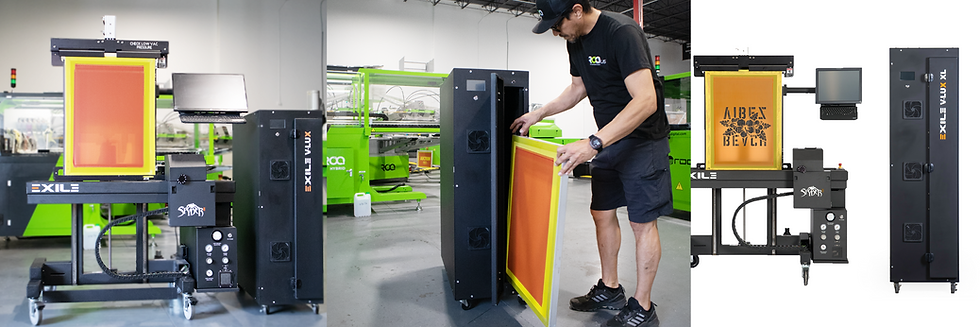
Print shops looking to understand options for the next step in their equipment evolution often find themselves scanning through fancy brochures and videos prompting the next great product. But what’s the real story behind the brochures and marketing hype that a print shop needs to know and consider before they upgrade?
One area that offers print shops greater efficiency and quality is in pre-press. Pre-press is the place to guarantee you have the best foundation for making great-looking and long-lasting quality products. This blog will dive deep into a few products in the pre-press department that may offer Printers a hyper-efficient leap forward for their business – computer-to-screen or CTS products and their accompanying exposure units.
For reference, EXILE Technologies, a multi-decade electronic pre-press equipment manufacturer based in Texas, designs and manufactures high-quality equipment for professional print shops. In this blog, we will weave together the facts on their SPYDER series of computer-to-screen products – SPYDER II and SPYDER III.
First, both SPYDER II and SPYDER III are intended for use in print shops with at least one automatic printing press that are looking to improve overall image quality and to speed the artwork transfer process to a screen, especially for a multiscreen job. More specifically, shops that see quick benefits from adding a SPYDER are generating anywhere from 10+ screens per day and want to improve halftone images and their process color work. Shops that are doing multi-colored prints will cut down on registration times which allows them to save time, increase efficiency, and potentially slot additional jobs in as needed.
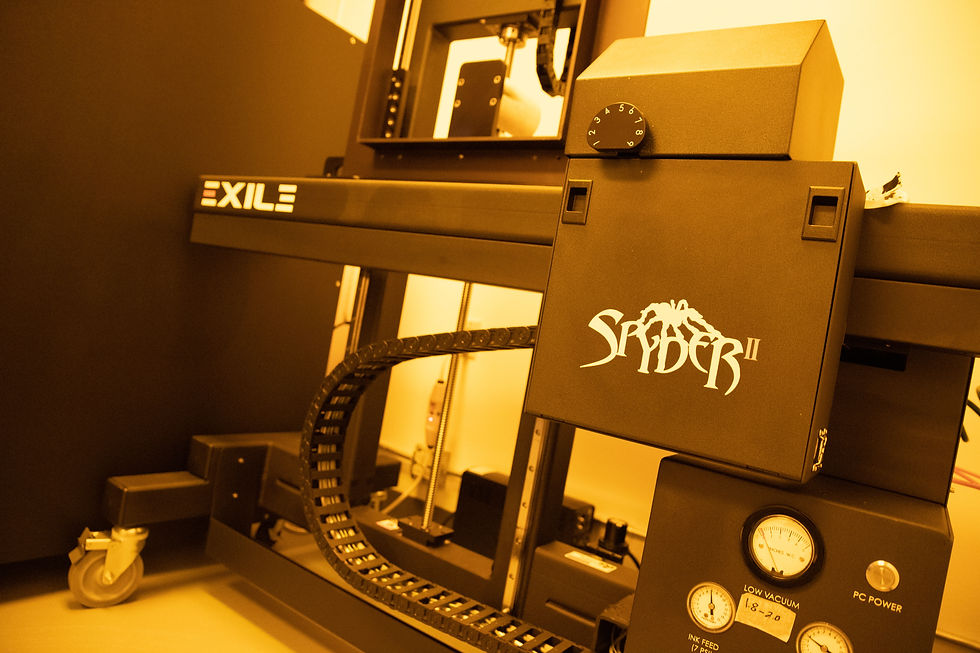
When comparing the SPYDERs side by side, Owners will want to know that a major difference between the two is their DPI. A key consideration in pre-press equipment selection is DPI, which refers to the number of actual dots per inch printed onto the substrate, in this case, the screen. SPYDER II offers 600 dpi in comparison to SPYDER III which boasts 1200 dpi. Industry insiders consider SPYDER II tireless in the textile printing industry. It’s fast and reliable with many satisfied Customers and years of performance under its belt. The newest product in the line, SPYDER III is more of a niche machine targeting specialty textile printers and industrial printing applications. The result, regardless of application, is smoother gradients at higher lines-per-inch, LPI, greater halftone detail, and noticeably improved edge definition.
Due to the nature of the technology differences, while the SPYDER II is incredibly accurate, the SPYDER III is more precise, still, and nearly perfectly accurate.
A subtle difference between the two SPYDERs is “Z” axis adjustment feature. SPYDER II has a manual adjustment in contrast to the SPYDER III infrared automated adjustment.
Using CTS machines reduces labor. It reduces labor in the art room by eliminating film printing. It reduces labor in the screen room by eliminating film positioning, exposure times, and pinhole touch-ups. The greatest savings, which relates to increased income, is in press setup time which directly translates to an increase in printing time.
There are other not often considered or discussed savings. A better footprint gives more space to other productive processes. It also provides ergonomic movement for the operator, improving efficiency even more. It eliminates the need, time, and resources to store, catalog, and search for films/screens. It is more cost-effective and efficient to reprint the screen on a SPYDER, having stored the artwork digitally, than to store films and screens, consume shop space, and spend time locating and reviewing old, pre-printed films and screens.
As opposed to liquid CTS machines where emulsions can play a part in print quality and exposure times, the SPYDERs are wax-based and therefore do not care what emulsion is being used.
On the topic of emulsion, EXILE also sells the V-LUX exposure unit built with CTS in mind. This unit uses a vertical design to allow for simple loading and unloading of a screen. It also features integrated rails to help ensure the proper exposure distance from the LED light source.

Time savings means money savings or better yet money making. Exposure units contribute to the savings as well with increased speed. By eliminating glass and vacuum, V-LUX shortens the overall cycle time and can reduce or eliminate screen touchups. A V-LUX unit can expose a screen in a very short time, 5-10 seconds, depending upon the type of emulsion. And, if the customer has a registration system compatible with SPYDER on the press, setup times can be reduced by as much as 40% or more. It’s worth noting the space savings and improved workflow transitioning associated with vertically oriented products such as V-LUX over traditional methods.
This blog has touched on key factors to consider inside the pre-press department to have a near-term, yet lasting impact on a print shop. Print quality, speed, efficiency, and equipment footprint top the list. All of these factors mean different things to different shops. Beyond just reading about features, it’s worth looking at the manufacturer’s longevity and reputation. In the case of EXILE, the company has been around for more than 30 years and makes products they back up with expert installation, set-up, and long-term support. Trust and reliability are intangible features to accompany all the cool features of equipment when deciding on important print shop upgrades.
For more information on how the SPYDER can slash Your setup times to seconds, click below to speak with Your ROQ Equipment Specialist:
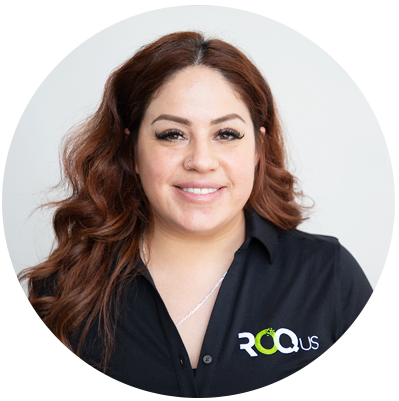
Comments